プラスチック射出成形プロセス

射出成形は、部品をプラスチックから製造する主な方法の1つです。 射出成形プロセスの最初のステップは、プラスチックペレットをホッパーに供給し、ホッパーがペレットをバレルに供給します。 バレルは加熱され、往復スクリューまたはラムインジェクターが含まれています。 往復ねじは通常、小さな部品を製造する機械に見られます。 レシプロスクリューがペレットを粉砕し、プラスチックの液化を容易にします。 バレルの前面に向かって、往復スクリューが液化プラスチックを前方に推進し、それによってプラスチックをノズルから空の金型に注入します。 バレルとは異なり、プラスチックを正しい形状に硬化させるために、金型は低温に保たれます。 モールドプレートは、大きなプレート(可動プラテンと呼ばれます)によって閉じられています。 可動プラテンは油圧ピストンに取り付けられており、金型に圧力をかけます。 型を閉じてクランプすることで、プラスチックが漏れ出して完成品に変形が生じるのを防ぎます。
プラスチック押出成形プロセス
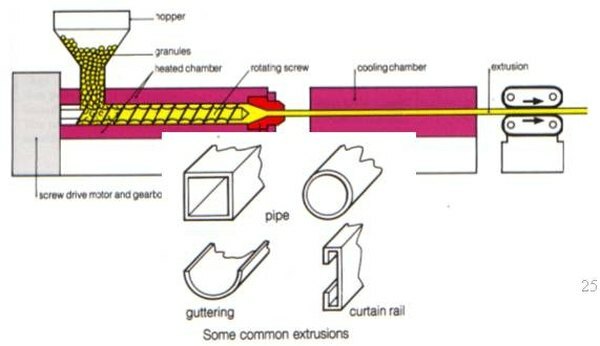
押出成形は、プラスチック部品を製造するもう1つの方法です。 押出成形は射出成形と非常によく似ており、パイプ、チューブ、ストロー、ホース、その他の中空部品の製造に使用されます。 プラスチック樹脂はバレルに供給され、そこで液化されます。 回転するスクリューが液化プラスチックを金型に押し込みます。金型にはチューブ状のオリフィスがあります。 チューブのサイズと形状によって、プラスチック片のサイズと形状が決まります。 次に、液化したプラスチックは冷却され、押出機に送られます。押出機はプラスチックを平らにし、最終的な形状に成形します。
プラスチック製造工程で発生する問題
プラスチックの製造プロセスでは、焼けた部品、変形、表面の欠陥、脆い部品など、さまざまな問題が発生する可能性があります。 金型を冷やさなかったり、バレル内の溶融温度が高すぎると、部品が焼けてしまいます。 さらに、レシプロスクリューが詰まったり、十分に速く回転しなかったりすると、液化した樹脂がバレル内に長く留まり、焦げてしまいます。 金型の表面温度が不均一である場合、金型が十分にしっかりと固定されていない場合、または溶融温度が高すぎる場合、表面の欠陥や変形が発生します。 十分な液化樹脂が金型に注入されていない場合、または金型を充填する前にプラスチックが硬化すると、脆い破片が形成されます。 プロセスがスムーズに実行されるようにするには、射出成形機と押出成形機の定期的なテストとキャリブレーションが重要です。