플라스틱 사출 성형 공정

사출 성형은 부품이 플라스틱으로 제조되는 주요 방법 중 하나입니다. 사출 성형 공정의 첫 번째 단계는 플라스틱 펠릿을 호퍼에 공급 한 다음 펠릿을 배럴에 공급하는 것입니다. 배럴은 가열되고 왕복 나사 또는 램 인젝터를 포함합니다. 왕복 나사는 일반적으로 더 작은 부품을 생산하는 기계에서 발견됩니다. 왕복 나사는 펠릿을 분쇄하여 플라스틱을 쉽게 액화시킵니다. 배럴 앞쪽으로 왕복 나사는 액화 플라스틱을 앞으로 밀어내어 플라스틱을 노즐을 통해 빈 금형에 주입합니다. 배럴과 달리 금형은 플라스틱을 올바른 모양으로 굳히기 위해 차갑게 유지됩니다. 몰드 플레이트는 큰 플레이트 (이동식 플래 튼이라고 함)에 의해 닫힌 상태로 유지됩니다. 이동식 플래 튼은 유압 피스톤에 부착되어 금형에 압력을가합니다. 몰드 셧을 클램핑하면 플라스틱이 누출되어 완성 된 조각에 변형이 생기는 것을 방지 할 수 있습니다.
플라스틱 압출 성형 공정
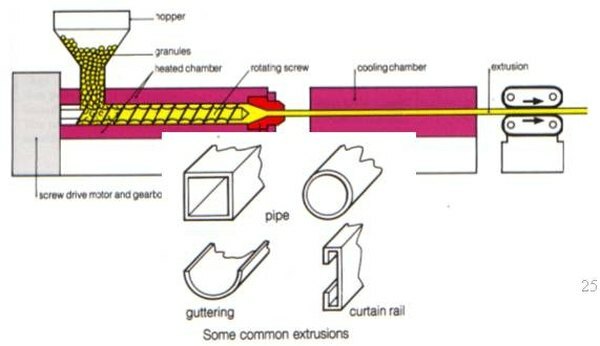
압출 성형은 플라스틱 부품을 제조하는 또 다른 방법입니다. 압출 성형은 사출 성형과 매우 유사하며 파이프, 튜브, 빨대, 호스 및 기타 속이 빈 조각을 만드는 데 사용됩니다. 플라스틱 수지는 액화되는 배럴에 공급됩니다. 회전하는 나사는 액화 플라스틱을 튜브 모양의 오리피스가있는 몰드로 밀어 넣습니다. 튜브의 크기와 모양에 따라 플라스틱 조각의 크기와 모양이 결정됩니다. 액화 플라스틱은 냉각되고 압출기를 통해 공급되어 플라스틱을 평평하게 만들고 조각을 최종 모양으로 만듭니다.
플라스틱 제조 공정에서 발생하는 문제
플라스틱 제조 공정 중에 연소 된 부품, 변형, 표면 결함 및 부서지기 쉬운 부품을 포함하여 여러 가지 문제가 발생할 수 있습니다. 금형이 차갑게 유지되지 않거나 배럴의 용융 온도가 너무 높으면 부품이 타 버립니다. 또한 왕복 나사가 막히거나 충분히 빠르게 회전하지 않으면 액화 수지가 배럴에 너무 오래 남아서 그을린 상태가됩니다. 금형의 표면 온도가 고르지 않거나 금형이 충분히 조여지지 않았거나 용융 온도가 너무 높으면 표면 결함 및 변형이 발생합니다. 금형에 액화 수지를 충분히 주입하지 않거나 금형을 채우기 전에 플라스틱이 굳어지면 취성 조각이 형성됩니다. 사출 및 압출 성형기의 정기 테스트 및 보정은 공정이 원활하게 진행되도록하는 데 중요합니다.